Experts in cutting area, including end mills, drills, reamers, saw, special cutters...etc.
Thursday, October 13, 2011
Wednesday, October 12, 2011
Indium tin oxide
Indium tin oxide is one of the most widely used transparent conducting oxides because of its two chief properties, its electrical conductivity and optical transparency, as well as the ease with which it can be deposited as a thin film. As with all transparent conducting films, a compromise must be made between conductivity and transparency, since increasing the thickness and increasing the concentration of charge carriers will increase the material's conductivity, but decrease its transparency.
Thin films of indium tin oxide are most commonly deposited on surfaces by electron beam evaporation, physical vapor deposition, or a range of sputter deposition techniques.
Common uses
ITO is mainly used to make transparent conductive coatings for liquid crystal displays, flat panel displays, plasma displays, touch panels, electronic ink applications, organic light-emitting diodes, solar cells, antistatic coatings and EMI shieldings. In organic light-emitting diodes, ITO is used as the anode (hole injection layer).
ITO has been used as a conductive material in the plastic electroluminescent lamp of toy Star Wars type lightsabers.[1]
ITO is also used for various optical coatings, most notably infrared-reflecting coatings (hot mirrors) for architectural, automotive, and sodium vapor lamp glasses. Other uses include gas sensors, antireflection coatings, electrowetting on dielectrics, and Bragg reflectors for VCSEL lasers.
ITO was used as a sensor coating in the later Kodak DCS cameras, starting with the Kodak DCS 520, as a means of increasing blue channel response.[2] It is reportedly used as a sensor coating in the Canon 400D/XTi and Sony Alpha DSLR-A100[citation needed].
ITO thin film strain gauges can operate at temperatures up to 1400 °C and can be used in harsh environments, e.g. gas turbines, jet engines, and rocket engines.[3]
[edit] Material and spectral properties
ITO is a heavily-doped n-type semiconductor with a large bandgap. Because of the bandgap, it is mostly transparent in the visible part of the spectrum. In the ultraviolet, it is opaque because of band-to-band absorption (a UV photon can excite an electron from the valence band to the conduction band). In the near infrared, it also opaque, because of free carrier absorption (an infrared photon can excite an electron from near the bottom of the conduction band to higher within the conduction band).
Alternatives
This section needs additional citations for verification. Please help improve this article by adding citations to reliable sources. Unsourced material may be challenged and removed. (April 2011)
Because of high cost and limited supply of indium, the fragility and lack of flexibility of ITO layers, and the costly layer deposition requiring vacuum, alternatives are being sought. Carbon nanotube conductive coatings are a prospective replacement.[4][5] As another carbon-based alternative, films of graphene are flexible and have been shown to allow 90% transparency with a lower electrical resistance than standard ITO.[6] Thin metal films are also seen as a potential replacement material. Inherently conductive polymers (ICPs) are also being developed for some ITO applications. Typically the conductivity is lower for conducting polymers, such as polyaniline and PEDOT:PSS, than inorganic materials, but they are more flexible, less expensive and more environmentally friendly in processing and manufacture. Other, inorganic alternatives include aluminium, gallium or indium—doped zinc oxide (AZO, GZO or IZO).
[edit] Constraints and trade-offs
This section does not cite any references or sources. Please help improve this section by adding citations to reliable sources. Unsourced material may be challenged and removed. (April 2011)
The main concern about ITO is the cost. ITO can be priced at several times that of aluminium zinc oxide (AZO). AZO is a common choice of transparent conducting oxide (TCO) because of cost and relatively good optical transmission performance in the solar spectrum. However, ITO does consistently defeat AZO in almost every performance category including chemical resistance to moisture. ITO is not affected by moisture and it can survive in a CIGS cell for 25–30 years on a rooftop. While the sputtering target or evaporative material that is used to deposit the ITO is significantly more costly than AZO, consider that the amount of material placed on each cell is quite small. Therefore the cost penalty per cell is quite small too.
[edit] Benefits
Surface morphology changes in Al:ZnO and i-/Al:ZnO upon dump heat (DH) exposure (optical interferometry)[7]
The primary advantage of ITO compared to AZO as a transparent conductor for LCDs is that ITO can be precisely etched into fine patterns.[8] AZO cannot be etched as precisely: It is so sensitive to acid that it tends to get over-etched by an acid treatment.[8]
Another benefit of ITO compared to AZO is that if moisture does penetrate, ITO will degrade less than AZO.[7]
[edit] Research examples
ITO can be used in nanotechnology to provide a path to a new generation of solar cells. Solar cells made with these devices have the potential to provide low-cost, ultra-lightweight, and flexible cells with a wide range of applications. Because of the nanoscale dimensions of the nanorods, quantum-size effects influence their optical properties. By tailoring the size of the rods, they can be made to absorb light within a specific narrow band of colors. By stacking several cells with different sized rods, a broad range of wavelengths across the solar spectrum can be collected and converted to energy. Moreover, the nanoscale volume of the rods leads to a significant reduction in the amount of semiconductor material needed compared to a conventional cell.[9]
引用出處:
http://en.wikipedia.org/wiki/Indium_tin_oxide
碧威為專業的刀具,銑刀,鎢鋼,切削刀具製造商,致力於製造優秀的產品,在客製化刀具方面的經驗十分豐富,並擅於幫助客戶解決各式各樣之刀具切削面臨之問題,對各種刀具材質切削刀具鍍模都非常瞭解透徹,可選用常見的鎢鋼及高速鋼或是近來詢問度極高的鑽石刀具。
碧威銑刀熱門產品為圓鋸片、鎢鋼刀、鋸片、木工鋸片、鎢鋼刀具及側銑刀。
機械類則有對刀具加工非常有幫助的冷風槍、渦流管槍,並有最新設計和技術的粉末成型機。
Tuesday, October 11, 2011
精密微小切削刀具的製備工藝
微小徑切削刀具的製備工藝是制約微細切削技術發展的難點之一。精密微細機械磨削和電火花線電極磨削(WEDG)、聚焦離子束濺射(FIB)等特種加工方法是目前主要的微細刀具製備技術。
(1)精密微小磨削工藝
磨削工藝是比較成熟的刀具製備和修整方法。微小刀具的精密磨削工藝主要採用金剛石砂輪,能夠實現高速鋼和硬質合金材料的高效成形。該工藝的要點是:為防止小直徑刀具折斷,應合理確定刃磨時的磨削壓力。通過對砂輪施加振動,可以顯著減小磨削力和最小成形直徑。
精密微小磨削工藝在一定程度上可以滿足微小切削刀具的製備要求,但受磨削力的影響,能夠穩定獲得的刀具最小直徑受到侷限。另外,刃磨工藝容易造成刀具表面劃痕和刃口缺陷,將直接影響加工表面質量和精度水平;磨削熱應力容易引起刀具表層微觀結構的變化;微小立銑刀的同心度和直徑偏離等製造誤差有可能大於微細切削的單齒進給量,成形精度有待提高。
(2)電火花線電極磨削工藝
電火花線電極磨削(WEDG)工藝的材料蝕除機理與普通電火花加工相同,電極和工件的運動原理為:線狀電極在導向器上連續移動,導向器沿工件徑向作微進給,而工件隨主軸旋轉的同時作軸向進給。該運動方式的主要優點是:線電極與工件之間為點接觸,容易實現微能放電;線電極始終沿導向器勻速運動,可以忽略線電極損耗對加工精度的影響。
通過控制工件的旋轉與分度,配合軸向的精密進給控制,WEDG工藝可以加工圓柱、圓錐、棱柱、螺旋槽、平面等多種截面形狀。該方法的主要優點是:刀具成形過程中無機械力作用,成形的尺寸精度和形狀精度較高,為微細刀具製備提供了一種有效方法。
(3)聚焦離子束濺射工藝
聚焦離子束濺射工藝是一種顯微加工技術,同樣可以用於微細刀具的製備,其基本原理為:選擇原子量較大的液態金屬鎵(原子量為69.72,其原子質量遠遠大於電子的質量)作為離子源,在離子柱頂端施加高密度的電場,形成數十keV的高能離子束,通過靜電透鏡將離子束聚焦為亞微米直徑的斑點,然後控制聚焦後的鎵離子束對工件進行轟擊,將鎵離子的動量傳遞給工件中的原子或分子,產生濺射效應從而實現材料的去除。通常每個入射鎵離子可以去除3~5個工件原子,可以精確控制材料的去除量。利用聚焦離子束濺射工藝,可以對硬質合金、高速鋼、單晶金剛石等材料進行顯微加工。
與精密磨削相比,基於聚焦離子束濺射的刀具成形過程沒有機械力的作用,刀具在製造過程中不會破損,能夠製備出具有極小特徵尺寸的微細刀具。
(4)激光加工工藝
為了克服聚焦離子束濺射工藝成形效率較低的問題,德國卡爾斯魯厄大學對採用激光加工工藝進行微小刀具製備進行了探索。該工藝同樣無機械力作用,加工過程中無振動,刀具不產生變形,加工成本較低。目前存在的問題是成形表面較粗糙,加工表面質量有待提高。
文章參考來源 - 三工數控工具
碧威為專業的刀具,銑刀,鎢鋼,切削刀具製造商,致力於製造優秀的產品,在客製化刀具方面的經驗十分豐富,並擅於幫助客戶解決各式各樣之刀具切削面臨之問題,對各種刀具材質切削刀具鍍模都非常瞭解透徹,可選用常見的鎢鋼及高速鋼或是近來詢問度極高的鑽石刀具。
碧威銑刀熱門產品為圓鋸片、鎢鋼刀、鋸片、木工鋸片、鎢鋼刀具及側銑刀。
機械類則有對刀具加工非常有幫助的冷風槍、渦流管槍,並有最新設計和技術的粉末成型機。
Monday, October 10, 2011
Friday, October 07, 2011
氧化銦錫介紹
氧化銦錫主要的特性是其電學傳導和光學透明的組合。然而,薄膜沉積中需要作出妥協,因為高濃度電荷載流子將會增加材料的電導率,但會降低它的透明度。
氧化銦錫薄膜最通常是用電子束蒸發、物理氣相沉積、或者一些濺射沉積技術的方法沉積到表面。
因為銦的價格高昂和供應受限、ITO層的脆弱和柔韌性的缺乏、以及昂貴的層沉積要求真空,其它取代物正被設法尋找。碳奈米管導電鍍膜是一種有前景的替代品。這類鍍膜正在被Eikos發展成為廉價、力學上更為健壯的ITO替代品。PEDOT和PEDOT:PSS已經被愛克發和H.C. Starck製造出來.PEDOT:PSS層已經進入應用階段(但它也有當暴露與紫外輻射下時它會降解以及一些其他的缺點)。別的可能性包括諸如鋁-參雜的鋅氧化物。
使用
ITO主要用於製作液晶顯示器、平板顯示器、電漿顯示器、觸摸屏、電子紙等應用、有機發光二極體、以及太陽能電池、和抗靜電鍍膜還有EMI屏蔽的透明傳導鍍膜。
ITO也被用於各種光學鍍膜,最值得注意的有建築學中紅外線-反射鍍膜(熱鏡)、汽車、還有鈉蒸汽燈玻璃等。別的應用包括氣體感測器、抗反射膜、和用於VCSEL雷射器的布拉格反射器。
ITO薄膜應力規可以在高於1400 °C及嚴酷的環境中使用,例如氣體渦輪、噴氣引擎、還有火箭引擎
物態 固體 熔點 1800-2200 K (1500-1900 °C) 密度 7120-7160 kg/m3 at 293 K 顏色 (粉末狀) 淺黃到綠黃色,取決於SnO2濃度 值隨成分改變.
引用出處:
http://zh.wikipedia.org/wiki/%E6%B0%A7%E5%8C%96%E9%93%9F%E9%94%A1
碧威為專業的刀具,銑刀,鎢鋼,切削刀具製造商,致力於製造優秀的產品,在客製化刀具方面的經驗十分豐富,並擅於幫助客戶解決各式各樣之刀具切削面臨之問題,對各種刀具材質切削刀具鍍模都非常瞭解透徹,可選用常見的鎢鋼及高速鋼或是近來詢問度極高的鑽石刀具。
碧威銑刀熱門產品為圓鋸片、鎢鋼刀、鋸片、木工鋸片、鎢鋼刀具及側銑刀。
機械類則有對刀具加工非常有幫助的冷風槍、渦流管槍,並有最新設計和技術的粉末成型機。
碧威是在刀具製造及機械工具業界中具有足夠水準的製造供應商!
Wednesday, October 05, 2011
刀具使用鈦合金切削之加工特點及刀材選用
鈦合金以優異的綜合力學性能、低密度以及良好的耐腐蝕性,被譽為是一種使人類走向太空時代的戰略性金屬材料,不僅在航空航天及軍工領域得到廣泛的使用,而且開始逐漸滲透到經濟生活的各個方面。隨著切削刀具產業的發展,鈦合金的加工技術受到更多的關注和研究。
鈦合金的分類
鈦合金按照不同的方法有不同的分類,最常用的分類方法是按退火後組織特點分類,可分成α、α+β、β型鈦合金
- α 型鈦合金密度小,有很好的熱強性和熱穩定性,銲接性能好,室溫、超低溫和高溫性能良好,但不能進行熱處理強化。例如TiAl在600°C時,仍然有很高的強度,而且蠕變性能、熱穩定性、疲勞性能和斷裂韌性等方面都有好的表現,常用於噴氣發動機渦輪盤和葉片的製造。
- α+β型鈦合金雙相合金,組織穩定,韌性、塑性和高溫變形性能隨著β相穩定元素的增加而提高;有較好的熱壓力加工性,能進行淬火時效使合金強化,熱處理後的強度約比退火狀態提高50% ~100% ;高溫強度高,可在400~500°C的溫度下長期工作,其熱穩定性次於α 鈦合金。α+β型鈦合金中Ti-6Al-4V是鈦合金中使用量最大的鈦合金,在美國,其產量佔鈦合金產量一半以上,以其優良的綜合力學性能和切削加工性大量用於航空零件製造。上圖為鈦合金航空發動機葉輪
- β鈦合金是β相固溶體組成的單相合金,室溫的強度較高,冷加工和冷成型加工能力強,未熱處理即具有較高的強度,淬火時效後合金強度得到進一步強化,室溫強度可達1372~1666MPa;但熱穩定性較差,不宜在高溫下使用
鈦合金切削加工的特點
鈦合金本身所具有的物理和化學性能給切削加工帶來了困難,具體表現有以下6點。
- 鈦合金的導熱性差,是不良導熱體金屬材料。由於導熱、導溫係數小,是45號鋼的1/6,所以在加工時所產生的高熱量不能有效擴散,同時刀具的切削刃和切屑的接觸長度短,使熱量大量聚集在切削刃上,溫度急劇上升,導致刀刃的紅硬性下降,刀刃軟化,加快刀具磨損
- 鈦合金的親和力大。鈦合金在加工中黏刀現象嚴重。增大了刀體與工件的摩擦,摩擦導致大量的熱,降低了刀具的使用壽命。
- 高的化學活性。在加工中,隨著切屑溫度的升高,容易與空氣中的O、N、CO、CO2、H2O 等發生反應,使間隙元素O、N的含量增加,工件的表面氧化變硬,難以加工,增大了刀具單位面積上所承受的切削力,刀尖應力變大,同時使前刀面和後刀面與工件的摩擦加劇,這將導致刀刃迅速磨損或崩刃
- 鈦合金的變形係數不大於1。在切削加工中,刀- 屑接觸面積小,增大了切屑和前刀面的摩擦,提高了切削溫度,加快了刀具前刀面磨損。
- 鈦合金的彈性模量小,在切削中容易產生較大變形、回彈、扭曲和振動,造成加工件幾何形狀和精度差,表面粗糙度增大,刀具磨損增加。
- 不同的加工方法,鈦合金的加工難度不同。按機械加工由易到難排序為:車削、銑削、鑽削、磨削。其中鑽小直徑深孔更困難
鈦合金切削加工的刀具材料
鈦合金加工的高成本是阻礙其廣泛使用的主要原因,尋求一種高效率、低成本的加工方法已成為當今鈦合金研究的熱點。刀具材料的選擇對於鈦合金的加工有很大影響。加工鈦合金的理想刀具材料必須同時具備較高的熱硬度,良好的韌性、耐磨性,高的導熱係數和較低的化學活性,在銑削時,刀具還應具有良好的抗衝擊性。
當今在生產實際中用來加工鈦合金的刀具材料主要有:硬質合金、聚晶金剛石(PCD) 、聚晶立方氮化硼(PCBN) 等。經過生產實際驗證,硬質合金和PCD刀具被認為是加工鈦合金比較理想的刀具材料
關於刀具材料選用..
- 硬質合金刀具
硬質合金刀具是目前加工鈦合金應用最為廣泛的一種刀具。因其低廉的價格、優良的導熱性、較高的硬度、韌性和紅硬性己成為國內企業加工鈦合金的首選。硬質合金按晶粒的大小可分為普通硬質合金、細晶粒硬質合金和超細晶粒硬質合金;按化學成分可分為鎢鈷類(YG)、鎢鈷鈦類(YT)和添加稀有碳化物類(YW)。由於鎢鈷鈦(YT)類刀具和鈦合金有強烈的親和力,所以目前在工業生產中獲得廣泛應用的仍然是鎢鈷類硬質合金YG8、YG6、YG3等。如果使用添加的稀有金屬的細晶粒硬質合金YA6、YD15、YG10H、YS2等,可提高刀具的壽命和加工效率。
硬質合金加工鈦合金速度可以達到45m/min以上,但當切削速度繼續增加時,刀具和工件接觸面的溫度迅速升高,同時由於Co的熔點較低,在高的切削溫度及元素擴散作用下,造成了刀具材料中W和Co元素的擴散和流失,降低了刀具的硬度和韌性,使硬質合金刀具發生嚴重的塑性變形、粘結磨損和擴散磨損,導致刀具失效,因此,硬質合金刀具只適合切削速度小於75m/min的鈦合金。
- 聚晶金剛石(PCD)刀具
聚晶金剛石刀具具有極高的硬度和耐磨性、刃口鋒利、低摩擦係數、高彈性模量、高導熱係數、以及與非鐵金屬親和力小等優點。
金剛石刀具主要有聚晶金剛石(PCD)刀具和化學氣相沉積刀具(VCD)金剛石刀具。金剛石類刀具適用於鈦合金的精加工和超精加工。金剛石的耐熱溫度只有700~800°C,加工時必須進行充分的冷卻和潤滑。試驗表明,在切削速度105m/min的情況下車削鈦合金Ti-6A1-4V時,PCD刀具並沒有發生粘結磨損,在刀具前、後刀面也都粘有較多鈦合金,這些粘著物會被切屑慢慢帶走,不會圖2硬質合金刀具對切削刃帶來損害,因為在刀具表面會形成一層薄薄的TiC層,這種TiC層很穩定,能很大程度降低PCD刀具前、後刀面的粘結和擴散磨損。但是由於PCD刀具刀尖鋒利和切削溫度高,在切削加工中更易發生微崩刃和石墨化引起的溝槽磨損。
- 聚晶立方氮化硼(PCBN)刀具
PCBN刀具的硬度雖然略低於金剛石,但卻遠遠高於其他高硬度材料,而且PCBN 刀具熱穩定比金剛石高得多,可達到1200°C以上,適合高溫干切削。另一個優點是化學惰性大,與鈦合金在1200°C不起化學反應。
PCBN刀具加工鈦合金與硬質合金刀具相比,有著切削速度高、表面粗糙度低和刀具壽命長等特點,並且在高速、低進給量、低背吃刀量的條件下,有更長的刀具壽命和非常好的工件加工表面粗糙度,因此PCBN刀具更適合用作鈦合金的精加工,但由於PCBN 刀具脆性很大,在切削加工中應重視刀具可能產生的破損和崩刃問題。
鈦合金切削加工的一般原則美國、日本、前蘇聯從20世紀60年代開始,由於軍事工業和飛機製造業的需要,開始對鈦合金的切削加工原則進行系統的研究,並獲得了大量的成果。鈦合金主要的切削原則有以下5 點。
- 切削速度:切削速度是影響刀刃溫度的重要因素。過高的切削速度會導致刀刃過熱、刀刃粘結和擴散磨損嚴重,刀具重磨頻繁,會縮短刀具壽命。同時會導致鈦合金工件表面層開裂或氧化,影響其力學性能,所以應在保證較大的刀具耐用度的前提下,選擇適當的切削速度,降低成本,保證加工質量。
- 進刀深度和走刀量:走刀量的變化對溫度的變化不大,所以降低切削速度增大走刀量是合理的切削方式。如果有氧化層和皮下氣孔層的情況,大的切深可以直接切到基體未氧化金屬層,提高刀具的壽命。
- 刀具的幾何角度:在切削鈦合金時選擇與加工方法相適應的前角和後角等幾何參數並對刀尖適當的處理,會對切削效率和刀具的壽命有重要的影響。試驗證明,當車削時為了改善散熱條件和增強切削刃,前角一般取5°~9°;為了克服因回彈而造成的摩擦,刀體的後刀面一般取10°~15°;當鑽孔時,縮短鑽頭長度、增加鑽心的厚度和導錐量,鑽頭的耐用度可提高好幾倍。
- 夾具的夾緊力:鈦合金易變形,夾緊力不能過大,特別在精加工工序時,可以選擇一定的輔助支承。
- 切削液:切削液是鈦合金加工中不可缺少的工藝潤滑油。切削液不僅可以有效降低切削溫度,減少刀具和切削摩擦產生的熱量,還可以充當切削過程的潤滑劑,減少鈦合金的切屑和刀具面的黏結,提高效率、降低成本,延長刀具的壽命。但不能使用含有氯或其他鹵元素和含硫的切削液,這類切削液會對鈦合金的力學性能產生不良影響。
結語..
綜上所述,鈦合金因其優良的性能在航空航天工業的使用比例逐年增加,但受切削加工成本高和加工效率低的影響,目前應用仍然受到較大限制。隨著刀具材料的研發和加工工藝的不斷完善,鈦合金的加工效率會大大地提高,加工成本將會明顯下降,從而在造船、汽車製造、化工、電子、海洋開發等領域擁有廣闊的應用前景。
文章參考來源 - 瀋陽理工大學機械工程學院
碧威為專業的刀具,銑刀,鎢鋼,切削刀具製造商,致力於製造優秀的產品,在客製化刀具方面的經驗十分豐富,並擅於幫助客戶解決各式各樣之刀具切削面臨之問題,對各種刀具材質切削刀具鍍模都非常瞭解透徹,可選用常見的鎢鋼及高速鋼或是近來詢問度極高的鑽石刀具。
碧威銑刀熱門產品為圓鋸片、鎢鋼刀、鋸片、木工鋸片、鎢鋼刀具及側銑刀。
機械類則有對刀具加工非常有幫助的冷風槍、渦流管槍,並有最新設計和技術的粉末成型機。
Tuesday, October 04, 2011
木工刀具(木工銑刀)如何選用?
木工刀具/銑刀選用的依據
- 被切削材料的性質
木材切削的對象是實木和木質複合材料。實木又可劃分為軟材、硬材和改性處理的木材等;木質複合材料包括膠合板、單板層積材、鉋花板、定向鉋花板、大片鉋花板、石膏鉋花板、水泥鉋花板、硬質纖維板、中密度纖維板、高密度纖維板、細木工板、膠合成材等。有些木材或木質複合材料工件還要經過單面或雙面貼面裝飾處理。 - 切削方向
實木切削時,根據刀刃相對木材纖維的方向將木材切削分為縱、橫、端向和縱端向、縱橫向和橫端向切削。 - 刀具回轉方向和進給方向
依據機床刀軸的回轉方向和木材工件進給的方向,確定刀具上刀刃的傾斜方向。 - 刀具與工件穩定性
刀具與工件在切削加工過程中的穩定性包括幾個方面的內容,工件的穩定性是指木材工件在切削加工中平穩進給而不發生跳動。加強工件穩定性採取的措施主要有降低工件重心和增大接觸面積。 - 加工表面質量要求
木材工件表面質量包括表面粗糙度、幾何尺寸和形狀位置精度。
木工刀具/銑刀的選用
- 確定銑刀的主要技術參數:
木工銑刀的主參數:刀具外徑,加工厚度,中心孔徑。
其它的技術參數:刀齒數,回轉方向,回轉速度,進給速度,夾持方式,刀齒材料。 - 選擇銑刀的結構形式
根據切削加工對象的性質和要求,從技術和經濟兩個方面綜合考慮選擇整體銑刀,銲接整體銑刀,裝配銑刀和組合銑刀。 - 銑刀回轉方向的選擇
銑刀回轉方向是依據加工機械主軸的回轉方向和刀軸與進給工件的相對位置確定的,無論是整體銑刀,還是裝配銑刀,切削刀刃相對銑刀半徑的傾角決定了銑刀的回轉方向。 - 銑刀切削用量的選擇
銑刀的切削用量包括銑刀的切削速度,工件的進給速度和銑削深度。銑刀的切削速度取決於銑刀轉速和銑刀的半徑。工件的進給速度取決於對切削加工表面質量的要求。被切削工件的表面粗糙度很大程度上取決於切削過程中銑刀每齒進給量,每齒進給量過大,加工表面過於粗糙,每齒進給量太小,加工表面會出現燒焦現象,因此銑刀的每齒進給量必須適當。 - 銑刀運轉的穩定性
銑刀運轉的穩定性是保證加工精度和加工表面質量的基礎。這包括兩方面的內容:一是銑刀在切削加工中由於受到外力激發而產生振動;二是銑刀在外力的作用下發生變形。 - 銑刀加工的安全性
銑刀加工的安全性包括銑刀回轉速度限制,屑片厚度限制,成型銑刀廓形高度限制和裝配銑刀刀片厚度與伸出量限制等。
木材切削加工的特點是高速度切削,銑刀的回轉速度多在3000rpm以上,高速切削為木材切削加工帶來的高生產效率和光潔的表面質量。同時,也帶來了一系列的安全問題,因此當銑削加工機床主軸轉速達到9000rpm時,除刀具小於16mm的柄銑刀外,應禁止使用裝配式銑刀,對於銲接整體銑刀的焊縫也進行嚴格的探傷檢查。
屑片厚度限制是保證銑刀進給量過大而引起銑刀嚴重過載必備的措施。
對於成型銑刀,成型輪廓廓形高度值與銑刀的夾持方式,切削工件厚度,銑刀的直徑有密切的關係。在切削加工工件厚度、銑刀直徑和中心孔徑確定以後,銑刀廓形高度反映了銑刀自身的強度和剛度,以及對切削阻力的承受能力。因此對廓形高度必須要有所限制,以保證銑刀使用時的安全。
裝配式銑刀刀體設計時必須要考慮刀片的夾持問題,無論是圓柱型的刀體還是圓盤型的刀體,刀片夾持形式必須保證可以提供足夠大的夾緊力以反抗回轉離心力。
文章參考來源 - 中國木材網
Monday, October 03, 2011
刀具材料-高速鋼的知識
高速鋼是一種含多量碳(C)、鎢(W)、鉬(Mo)、鉻(Cr)、釩(V)等元素的高合金鋼,熱處理後具有高熱硬性。當切削溫度高達600°C以上時,硬度仍無明顯下降,用其製造的刀具切削速度可達每分鐘60米以上,而得其名。高速鋼按化學成分可分為普通高速鋼及高性能高速鋼,按製造工藝可分為熔煉高速鋼及粉末冶金高速鋼。
普通高速鋼
- 高速鋼是製造形狀複雜、磨削困難的刀具的主要材料。
- 普通高速鋼可滿足一般需求。常見的普通高速鋼有兩種,鎢系高速鋼和鎢鉬系高速鋼。
- 鎢系高速鋼熱處理硬度可達63-66HRC,抗彎強度可達3500MPa,可磨性好。
- 鎢鉬系高速鋼目前正在取代鎢系高速鋼,具有碳化物細小分佈均勻,耐磨性高,成本低等一系列優點。熱處理硬度同上,抗彎強度達4700MPa,韌性及熱塑性比w18Cr4V提高50%。常用於製造各種工具,例如鑽頭、絲錐、銑刀、鉸刀、拉刀、齒輪刀具等,可以滿足加工一般工程材料的要求。只是它的脫碳敏感性稍強。
高性能高速鋼
高性能高速鋼具有更好的硬度和熱硬性,這是通過改變高速鋼的化學成分,提高性能而發展起來的新品種。它具有更高的硬度、熱硬性,切削溫度達攝氏650度時,硬度仍可保持在60HRC以上。耐用性為普通高速鋼的1.5-3倍,適用於製造加工高溫合金、不銹鋼、鈦合金、高強度鋼等難加工材料的刀具。
主要品種有4種,分別為高碳系高速鋼、高釩系高速鋼、含鈷系高速鋼和鋁高速鋼。
高碳系高速鋼
因含碳量高(0.9%),故硬度、耐磨性及熱硬性都比較好。用其製造的刀具在切削不銹鋼、耐熱合金等難加工材料時,壽命顯著提高,但其抗彎強度為3000MPa,衝擊韌性較低,熱處理工藝要求嚴格。
高釩系高速鋼
含釩量達3-4%,使耐磨性大大提高,但隨之帶來的是可磨性變差。高釩系高速鋼的使用及發展還需要依賴於磨削工藝及砂輪技術的發展。
鈷高速鋼
其特點為:含釩量不高(1%),含鈷量高(8%),鈷能促使碳化物在淬火加熱時更多地溶解在基體內,利用高的基體硬度來提高耐磨性。這種高速鋼硬度、熱硬性、耐磨性及可磨性都很好。熱處理硬度可達67-70HRC,但也有採取特殊熱處理方法,得到67-68HRC硬度,使其切削性能(特別是間斷切削)得到改善,提高衝擊韌性。鈷高速鋼可製成各種刀具,用於切削難加工材料效果很好,又因其磨削性能好,可製成複雜刀具,國際上用得很普遍。但中國鈷資源缺乏,鈷高速鋼價格昂貴,約為普通高速鋼的5-8倍。
鋁高速鋼
主要加入鋁(Al)和矽(Si)、鈮(Nb)元素,來提高熱硬性、耐磨性。適合中國資源情況,價格較低。熱處理硬度可達到68HRC,熱硬性也不錯。但是這種鋼易氧化及脫碳,可塑性、可磨性稍差,仍需改進。國際市場上高性能高速鋼使用量已經超過普通高速鋼25-30%。
粉末冶金高速鋼
粉末冶金高速鋼及其製品
近幾年來高速鋼的最大變革就是發展了粉末冶金高速鋼,它的能優於熔煉高速鋼。用高壓氬氣或氮氣霧化熔融高速鋼水,得到細小高速鋼粉末,篩選後為0.4mm以下的顆粒;在真空(0.04Hg)狀態下,密閉燒結達到密度65%;再在1100°C高溫、300MPa高壓下製成密度100%的鋼坯,然後鍛軋成鋼材,這樣有效地解決了熔煉高速鋼在鑄錠時要產生粗大碳化物偏析的問題,而它無論截面多大,其碳化物級別均為一級。碳化物晶粒極細,小於0.002mm,而熔煉高速鋼碳化物晶粒為0.008-0.02mm。
粉末冶金高速鋼具有良好的力學性能,適合製造:間斷切削條件下易崩刃的刀具、強度高而切削刃又必須鋒利的刀具,如插齒刀、滾刀、銑刀,高壓動載荷下使用的刀具。
它的碳化物偏析小,晶粒細,可磨性好,適合製造:大尺寸刀具、精密刀具、複雜刀具。這類材料的高溫熱硬度高,又適合製造難加工材料所用的刀具,確實是面面俱到。
粉末冶金高速鋼生產過程較複雜,造價較高。中國鋼廠提供的品種較少,市場用量也很少。國際上著名鋼廠如美國Crucible公司已可提供近二十種粉末冶金高速鋼,日本神戶制鋼所、日立金屬公司均可提供近十種粉末冶金高速鋼,供應量也在迅速增長。日本著名的OSG公司用粉末冶金高速鋼製造了鑽頭、銑刀、絲錐,NACHI公司製造了滾刀、插齒刀、剃齒刀。有理由相信技術性能高的粉末冶金高速鋼將會得到更廣泛的應用,為金屬加工業帶來新的發展。
高速鋼的市場定位及發展趨勢
高速鋼材料按製造工藝可分為熔煉高速鋼及粉末冶金高速鋼。
自二十世紀初發現高速鋼以來,對現代工業發展起到了重要作用。可以說沒有高速鋼,就沒有現代的金屬加工業。儘高速鋼管六十年代起,硬質合金等材料崛起,但是對於製造形狀複雜、磨削困難的刀具,如拉刀、剃齒刀、插齒刀等,始終處於主導地位。特別是要求刀具具備高韌性時,就非高速鋼莫屬了。
高速鋼的主要應用領域是機械和工具製造業,必然要適應這個行業的發展,近幾年來機械加工採用了高速度的數控機床,例如加工中心、車削中心等,金屬切削速度越來越快,要求刀具必須具有高速使用性能,即熱硬性、耐磨性、衝擊韌性要好,因此,廠家紛紛研發符合上述要求的高速鋼材料。
在機加工費用中,材料約占15-20%,刀具約占25-35%。用戶對刀具的選用也越來越趨向合理,即選用性能與價格比好的刀具。
高速鋼刀具占主導地位的領域,如精密零件、複雜零件、成形加工零件的市場也越來越大,對可磨性的要求也越來越高。
高速鋼-走過一個世紀的鋼種,應瞄準特定市場空間,提高自身技術含量,去抗衡其他材料的挑戰。
文章參考來源 - 易展模具
碧威為專業的刀具,銑刀,鎢鋼,切削刀具製造商,致力於製造優秀的產品,在客製化刀具方面的經驗十分豐富,並擅於幫助客戶解決各式各樣之刀具切削面臨之問題,對各種刀具材質切削刀具鍍模都非常瞭解透徹,可選用常見的鎢鋼及高速鋼或是近來詢問度極高的鑽石刀具。
碧威銑刀熱門產品為圓鋸片、鎢鋼刀、鋸片、木工鋸片、鎢鋼刀具及側銑刀。
機械類則有對刀具加工非常有幫助的冷風槍、渦流管槍,並有最新設計和技術的粉末成型機。
Sunday, October 02, 2011
銑刀的選用 Part-2
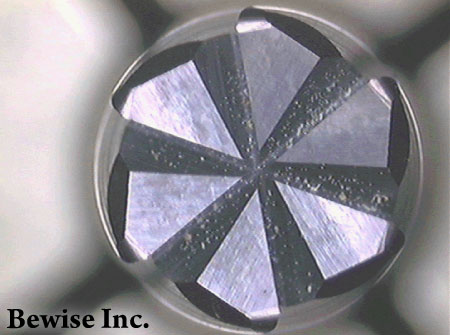
繼上一篇介紹銑刀的選用後,這篇要繼續介紹以銑刀之外型與用途分類。
以銑刀之外型與用途分類,可分為平銑刀、側銑刀、角銑刀、型銑刀、端銑刀、T型槽銑刀、半月鍵座銑刀、鳩尾槽銑刀、以及面銑刀。
- 平銑刀(plain milling cutter):
在圓筒形的圓周上製出切削刃,以用來銑切工件的水平面者,稱為平銑刀。下圖a之銑刀的切削刃與軸線平行者適用於輕銑削用,因銑削時切屑會全部進入切屑槽內,使銑刀跳動,故不適於重切削。(b)圖與(c)圖之切削刃為螺旋形,銑削時可有一個以上的切刃同時與工作面接觸,切削狀況較穩定。(b)圖之螺旋角較大,對切屑有較佳的剪斷作用,可減少銑切時震動,產生較光滑的平面,故可用在粗重切削或硬材料之切削。(c)圖之螺旋角較小,適於作中切削量的銑切或精光工作表面用。
(a)輕型平銑刀
(b)重切削用平銑刀
(c)精切削用平銑刀
- 側銑刀(side milling cutter):
側銑刀因其側面也有切刃而得名,依刀刃分佈的情形可分為平面側銑刀、半側銑刀、交錯刀刃側銑刀及聯鎖側銑刀四種,如下圖所示。
平面側銑刀(如下圖(a)所示)在圓周上及兩側均有刀刃,可用於銑槽、銑平面及騎銑。
半側銑刀(如下圖(b)所示)在圓周上及單側上佈有刀刃,用於重銑削端面。側面的刀刃可在左側或右側,故若以左右側銑刀各一,中間裝置一平銑刀,則可作排銑工作。
若切刃在兩側面上依次交錯出現,螺旋角亦相對交錯者稱交錯刀刃側銑刀(如下圖(c)所示),可使銑削力降低,震動減少,常用於溝槽之高速及深進刀銑切。
如下圖(d)所示為聯鎖側銑刀,係將左、右側銑刀合併成一體,圓周上的刀刃斜角亦相對,則使軸向推力相互抵消,可作正確的溝槽銑削工作。
(a)平面
(b)半側銑刀
(c)交錯側銑刀
(d)聯鎖側銑刀
- 角銑刀(angular cutter):
切刃既不平行亦不垂直於銑刀軸之銑刀稱為角銑刀。可分為單側角銑刀及雙側角銑刀,如下圖所示,用於銑削角面,如V 形溝槽、鋸齒狀、斜面及鉸刀刃齒等。
單側角銑刀之切刃在圓錐面上,平面上可以有切刃或無切刃,亦可在左側或右側(如下圖a所示)。平面與錐面所成的角度即為銑刀稱呼角度,如45°、50°、60°、70°、80°等。
雙側角銑刀之切刃在兩相交的錐面上,兩側之角度可以相等或不相等(如下圖(b)所示)。如兩邊角度相等則以夾角大小稱呼之,如45 ° 、60 ° 、或90° 等,如兩邊角度不相等則以各角度大小稱呼之,如12 ° 〜53 ° 、120 ° 〜58 °、12 ° 〜63 °、120 ° 〜68 ° 、或12°〜730°等。
(a)單側角銑刀
(b)雙側角銑刀
- 切割銑刀(metal slitting saw):
用於銑切狹槽或切割金屬之銑刀稱切割銑刀,如下圖所示:
- 型銑刀(formed cutter):
依銑刀切刃外型,銑出與其相反形狀之工件,適合於大量生產用,下圖所示者為三種常用之型銑刀,即銑削半圓凹面的凸面銑刀(convex milling cutter,下圖(a)所示)、銑削半圓凸面的凹銑刀(concave milling cutter,如下圖(b)所示)及銑削齒輪用的齒輪型銑刀(如下圖(c)所示)。
(a)凸面型銑刀
(b)凹面型銑刀
(c)齒輪型銑刀
- 端銑刀(end mill):
端銑刀的端面及周邊上均有切刃,端面上的切刃作用有如鑽頭,周邊之切刃有如豎立的平銑刀,故端銑刀可用於銑削平面、溝槽、輪廓等。
如下圖(a)所示為直柄端銑刀,通常使用彈簧筒夾夾持(如下圖(c)所示)。下圖(b)所示為錐柄端銑刀,有標準的(NC)或白氏(B & S)標準等視其尺寸大小可直接套於銑床主軸孔或刀軸孔。套殼端銑刀形狀與側銑刀類似,其外徑一般為50mm 以上,需使用刀柄安裝(如下圖(d)所示)。
(a)直柄端銑刀
(b)錐柄端銑刀
(c)端銑刀夾頭
(d)套殼銑刀刀軸
端銑刀周邊切刃通常具有螺旋線,可使切削較穩定。其切刃數可有二、三、四、六切刃等形式,二切刃銑刀之兩溝槽在端面相交成兩切刃口通過中心線(如下圖左所示),使端銑刀猶如鑽頭可直接對工件鑽孔。當鑽孔深度不超過銑刀半徑時,就可利用圓周面之刀齒直接銑溝槽。四刃端銑刀之端面有中心孔(如下圖右所示),不能以端面之切齒直接鑽孔,只能利用圓周之刃齒從工件邊銑削。
- T型槽銑刀(T-slot cutter):
兩側面及圓周面均有刀齒,並具有標準錐柄可套入接頭再裝入主軸。以端銑刀或側銑刀在工件上銑削一垂直狹槽後,再用T 型槽銑刀在底部銑創較寬的水平槽,即成為T 型槽(如下圖所示)。T 型槽銑刀刃部寬為3〜10mm,直徑為10〜50mm。
- 半月鍵座銑刀(woodruff keyseat cutte):
與側銑刀相似,但僅圓周面上有切刃,且具有刀柄,用於銑切工件軸上的半月型鍵座,如下圖所示。
- 鳩尾槽銑刀(dovetail milling cutter):
用以加工鳩尾座及鳩尾槽的銑刀,如下圖所示。
- 面銑刀(face milling cutter):
面銑刀很像套殼端銑刀,但面銑刀外徑在150nm 以上,利用套桿裝在銑床主軸口,面銑刀用於銑平面其工作類似龍門鉋床。面銑刀圓周上刀齒作主要銑削工作,而平面上刀齒作精削修光工作。下圖(a)所示為高速度鋼刀片之面銑刀盤,下圖(b)為裝碳化鎢刀片之面銑刀盤。
(a)高速鋼面銑刀盤
(b)碳化鎢面銑刀盤
綜合上一篇來說:
- 一般銑刀的材料與使用的場合如下
- 高速鋼銑刀:適合一般用途,使用最廣。
- 碳化物銑刀:適合高速切削。
- 非鐵金屬鑄造合金銑刀:適合重切削。
- 端銑刀的刀柄有以下兩種形式
- 直柄端銑刀
- 錐柄端銑刀
- 常見的成形銑刀如下
- 凸面型銑刀
- 凹面型銑刀
- 齒輪型銑刀
- 鳩尾座銑刀
- 半月鍵銑刀
文章參考來源 - 職業訓練局
碧威為專業的刀具,銑刀,鎢鋼,切削刀具製造商,致力於製造優秀的產品,在客製化刀具方面的經驗十分豐富,並擅於幫助客戶解決各式各樣之刀具切削面臨之問題,對各種刀具材質切削刀具鍍模都非常瞭解透徹,可選用常見的鎢鋼及高速鋼或是近來詢問度極高的鑽石刀具。
碧威銑刀熱門產品為圓鋸片、鎢鋼刀、鋸片、木工鋸片、鎢鋼刀具及側銑刀。
機械類則有對刀具加工非常有幫助的冷風槍、渦流管槍,並有最新設計和技術的粉末成型機。